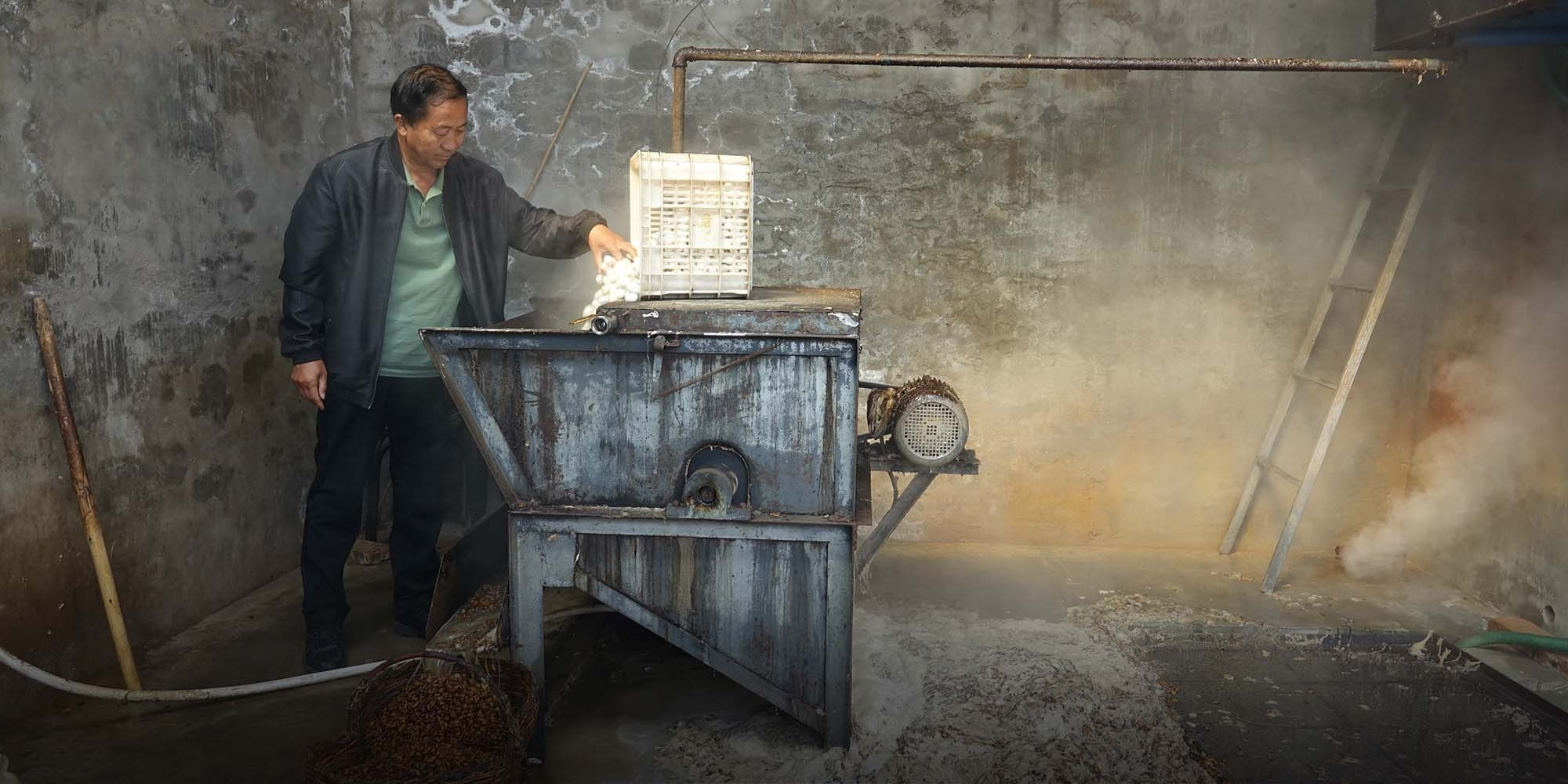
In a Rural Chinese County, Progress Is Measured by the Worm
SHAANXI, Northwest China — Inside a steam-filled workshop, Zhang Wurong is working furiously to feed mountains of cocoons into a silk-reeling machine.
The machine allows the 59-year-old to harvest silk on an industrial scale. It uses boiling water to strip the cocoons from the silkworms inside, then processes the cocoons into silk cloth, before spewing out the worms along with the wastewater.
Before, Zhang had to strip and unwind each cocoon manually — a severe limitation given how little time he has to collect the silk. Silkworms take only 12 days to spin their cocoons, and the fiber spun during the first seven days isn’t usable, he says.
“I have only around five days to process all the cocoons,” Zhang tells Sixth Tone. “If the worm bites a hole and flies out, the cocoon is broken and you can’t pull out good silk.”
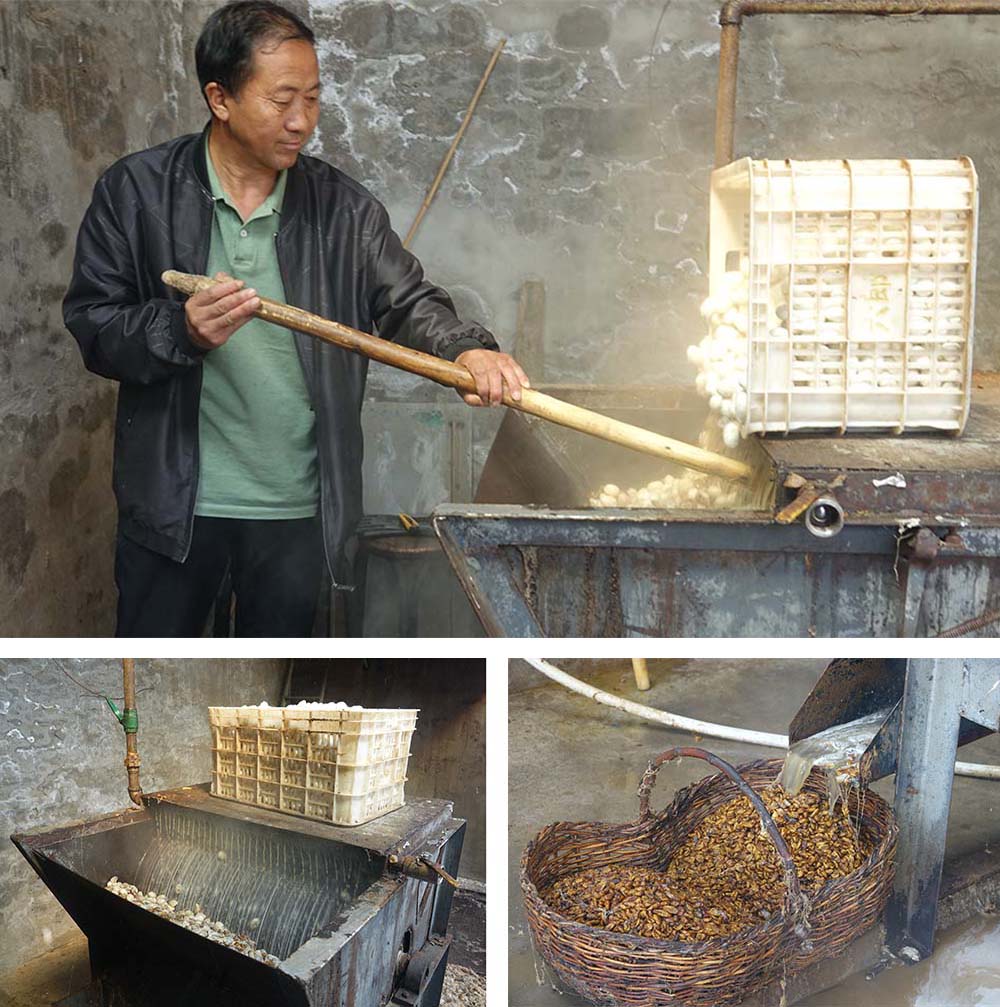
In this corner of northwest China’s Shaanxi province, silkworms are serious business. Many locals see the insect as their ticket to prosperity.
Wubu County, where Zhang lives, is farming country. For centuries, locals have eked out a living raising crops that suit the region’s dry climate, including corn and jujube. But during the Qing Dynasty (1644-1912), farmers here also began boosting their incomes by rearing silkworms in their spare time.
For a long time, silk production was just a side gig for Wubu’s farmers — a way to make a little extra money during the slack season. However, as China’s economy began booming in the late 20th century, officials began to see silk as potentially a huge local money-spinner.
As in so many parts of rural China, Wubu’s attempts to develop a lucrative new industry has been a painstaking, decadeslong project. Progress has been hard-won, setbacks frequent. Yet, inch by inch, the county has moved toward its goal.
In Wubu, the main problem is the climate. Unlike in the eastern provinces of Jiangsu and Zhejiang, the traditional center of China’s silk industry, silkworms can’t be raised all year round here. The worms feed on mulberry leaves, but mulberry trees in Wubu only produce enough leaves to nourish the insects during late spring and early fall.
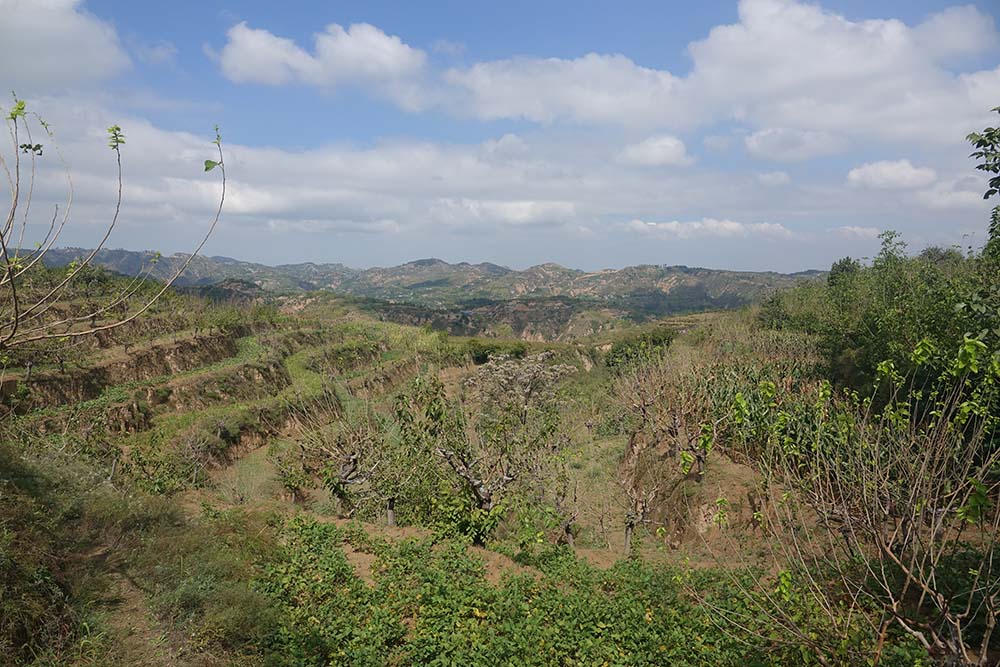
For this reason, the whole county has to work together to maximize productivity during these peak seasons, trying not to waste a single cocoon.
Starting from the 1980s, local authorities began implementing a collective silk production model — an approach rooted in China’s planned economy era. The aim was to transform silkworm-rearing from a casual, household activity into a large-scale industry. A local agriculture research institute was put in charge of rearing and distributing all the county’s silkworms, ensuring that the worms have a standardized life cycle, Zhang says.
“The institute will take the eggs out of cold storage on a specific day according to the weather forecast and the growing conditions of the mulberry leaves,” he says. “Those eggs are then transported to the designated rural areas to start their life cycle of nearly one month.”
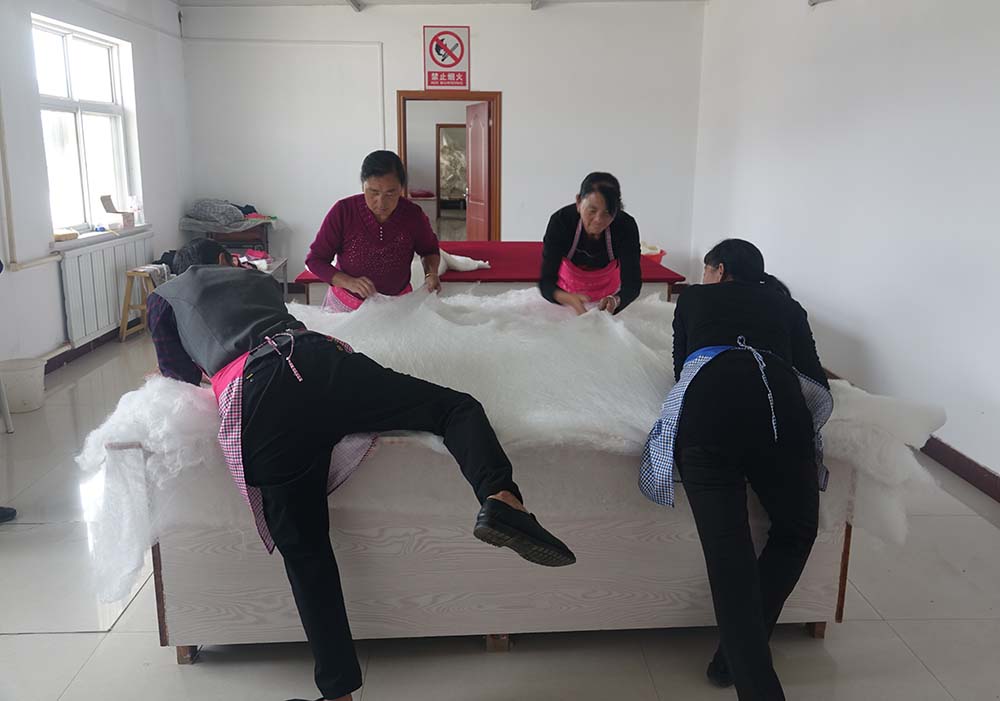
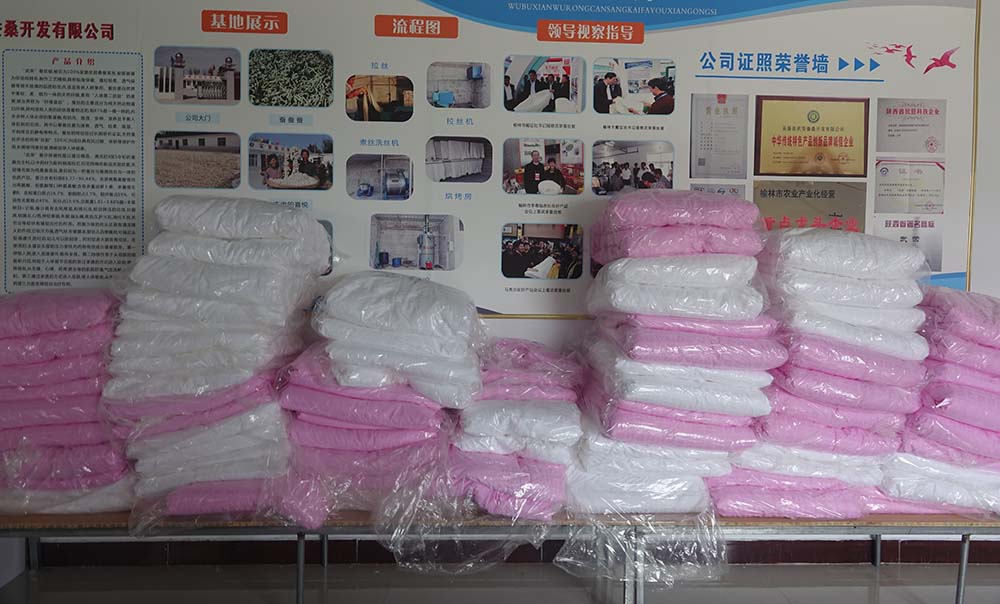
The approach is paying off. In 2021, Wubu raised over 2 million silkworms, a 50-fold increase over 2013. The worms produced 39 tons of cocoons, generating a total income of 2.3 million yuan for the county, according to official data.
The gains have helped Wubu raise itself out of extreme poverty. The county’s residents now have 18,200 yuan of annual disposable income on average, according to official data. Middle-class comfort is still a long way off, but they’re now comfortably above China’s poverty threshold.
This year, local officials have offered farmers greater subsidies to try sericulture, which has convinced more people to join the industry, Zhang says. The outlook for other industries looks less promising: There is little available land in this mountainous region to expand corn planting, while the market for jujube is already oversupplied.
“The standardized and industrialized silkworm rearing and processing industry is one of the main ways for Wubu County to achieve poverty alleviation,” he says.
A 64-year-old local farmer, surnamed Xing, tells Sixth Tone that he just had the most productive year of his life rearing silkworms. He produced 35 kilograms of cocoons this year, selling them to Zhang for 40,000 yuan.
“The more you raise, the more subsidies you get,” says Xing, adding that he received nearly 5,000 yuan of subsidies.
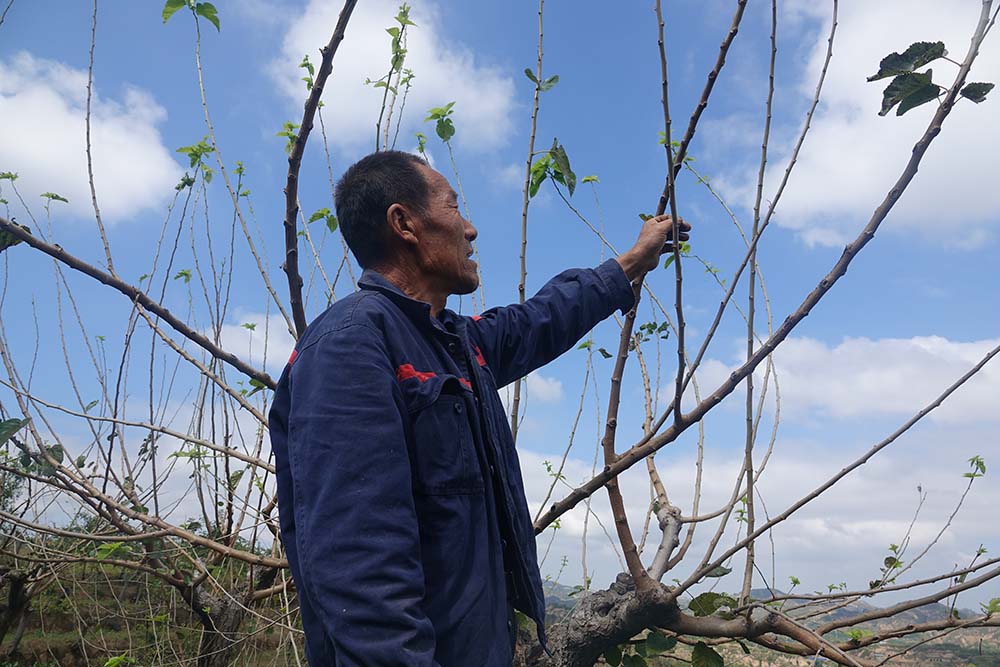
Zhang has been working with the local agriculture bureau to guide farmers raising silkworms since 1983. It hasn’t always been plain sailing. In the 1990s, the price of silkworm cocoons kept falling for several years, causing many local farmers to abandon the industry and go and find work in the cities.
That experience taught Zhang a lesson: It’s not enough to raise silkworms; the county also needs to find a way to sell finished silk products, which produce higher profits. He was determined to set up his own factory.
“If we can invest in high-tech equipment, we can improve the quality of our silk and increase the value of our silk products,” Zhang says.
In the 2000s, Zhang did just that. He invested in some silk processing machines, set up his own business, and began buying cocoons from Wubu’s farmers, paying a premium on the government’s unified purchase price. Then, in 2013, he finally managed to open his own 3,000-square-meter factory to produce silk quilts.
The factory required an investment of 3 million yuan, but Zhang says it has been worth the money. It generated 3 million yuan of revenues in just its first two years of operation, with Zhang making a 30% profit.
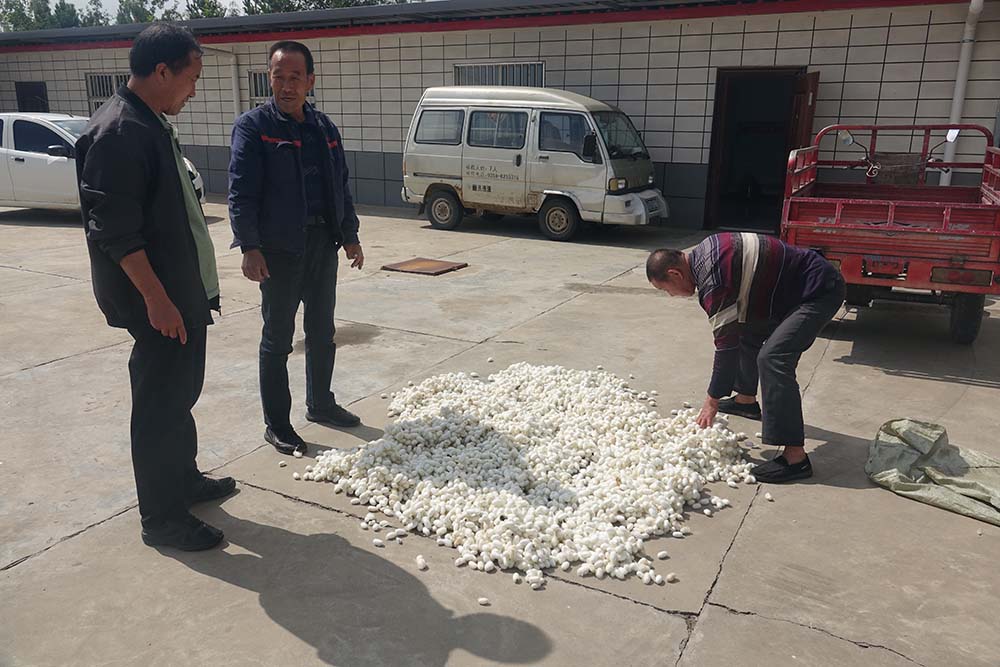
The secret to this success, Zhang says, has been using the silk to produce a finished product: silk quilts. Before, Wubu’s silk was sold as a raw material to high-end silk scarf factories, which was far less profitable.
Zhang would like to set up his own scarf factory one day, but that would require an investment of more than 100 million yuan. Silk quilts are an unusual product, he says, but they’re still selling well.
“The whole industry believes that the best silk must be used to make silk scarves to get the highest returns, while the inferior silk is for silk quilts,” says Zhang. “But I managed to find many clients willing to buy this kind of quilt.”
A 2-kilogram silk quilt sells for 2,000 yuan, Zhang says. Most of his clients are from Shaanxi and the neighboring Shanxi province and Ningxia Hui autonomous region.
“Many have said to me that it’s overkill to use the best silk to produce a quilt,” Zhang says. “But I have my own financial ledger in mind.”
Editor: Dominic Morgan.
(Header image: Silk factory owner Zhang Wurong feeds cocoons into a silk-reeling machine, in Yulin, Shaanxi province, Sept. 20, 2022. Wu Peiyue/Sixth Tone)