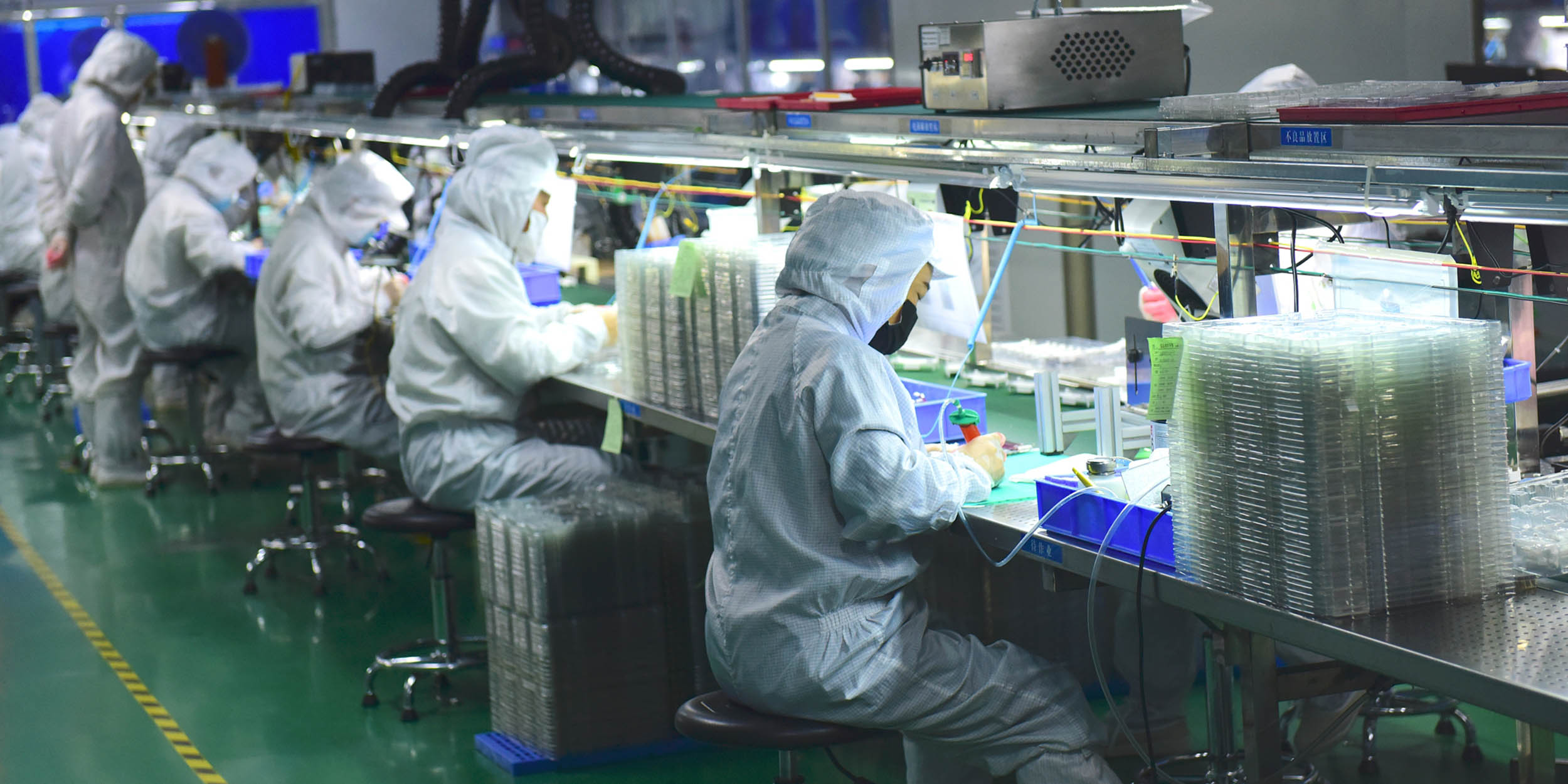
What’s Keeping China From Moving Up the Value Chain?
Over the past few decades, China’s low labor costs helped transform it into the “world’s factory,” a center of industrial production for companies around the globe.
Now, with wages rising, the workforce shrinking, and the global supply chain undergoing a significant reshuffle, China faces an even stiffer challenge: upgrading its labor-intensive low-end manufacturing industries to better compete in the world of value-added manufacturing.
Most discussions of this upgrade tend to focus on the adoption of cutting-edge technologies like artificial intelligence and automation. But what about the workforce?
Fantasies of a post-labor industrial landscape aside, these new technologies will ask a lot of workers, and it’s increasingly apparent that China doesn’t have the pool of skilled staff necessary to move up the value chain. There are a number of reasons for this, starting with high turnover rates and unstable labor relations that prevent workers from effectively acquiring new skills. Life for many Chinese industrial workers is characterized by instability: They’re constantly switching jobs, companies, and even cities. A decade ago, manufacturers in the Pearl River Delta, one of China’s most prosperous manufacturing hubs, reported that as many as 20% to 30% of new employees leave within three months of their recruitment. More recent government data suggests turnover is rising.
High turnover rates make it harder for employees to hone their skills. Contributing to poor employee retention is China’s hukou household registration system, which effectively locks migrants out of public services in their city of residence. Housing is another major problem. While conducting fieldwork in a major Chinese city, we found that close to 60% of industrial workers are in a precarious living situation, characterized by poor housing, insufficient living space, or a lengthy commute. Housing prices have skyrocketed in Chinese cities over the past decade, while the urban villages that once offered affordable and accessible accommodation to migrant workers are being torn down and moved to the outskirts.
Precarious living circumstances often push workers into more flexible forms of employment. Deprived of stable housing and discriminated against by urban welfare systems, migrant workers have no way of putting down roots in the city, which in turn makes it hard for them to receive long-term technical training from a single employer.
For their part, manufacturers have embraced “flexible” employment systems such as seasonal employment, contract labor, and shared employee pools.
Although this helps companies cut down on labor costs, it disrupts industrial workers’ development. China is reliant on employers to train and accredit workers: In one of my past surveys of industrial workers, 67.1% of respondents said their technical training was provided by their employer, while only 19.9% received training at private institutions or vocational colleges. However, because employers assume skilled employees will be poached by their rivals, many small- and medium-sized enterprises are unwilling to invest in employee training. In our survey of companies, we discovered that 61% hadn’t established internal training programs.
Meanwhile, the government and employers cannot agree on a training model. Both companies and the government have their own certification systems, and each side refuses to recognize the other. This means that government-issued certificates — which tend to overemphasize cultural and theoretical knowledge — rarely translate into better wages for industrial workers, while the government is often skeptical of funding certificate programs created by companies or industry associations.
When industrial workers do acquire useful skills, it rarely translates into higher social status. Even skilled factory workers are at a huge disadvantage compared to their white-collar counterparts when it comes to wages, access to basic public services, and applying for a hukou.
Their career prospects are similarly limited. In manufacturing, there are only a few pathways for promotion open to the rank and file, and none of them lead very far. My research suggests that, although there is a significant demand among Chinese industrial workers for vocational training, the vast majority aren’t interested in studying skills applicable to their current job. Rather, they’d prefer to receive academic education or business training. This is perhaps a reflection of how underappreciated and dissatisfied they feel in their current positions.
When it comes to upgrading China’s industrial base, investing in technological progress such as automation and artificial intelligence isn’t enough. We must acknowledge that millions of industrial workers will still be needed to support Chinese manufacturing, and that their skill level will determine the success or failure of any effort to reform the national economy.
Facilitating workers’ acquisition of new skills will require the cooperation of workers themselves, as well as that of government departments, companies, and vocational colleges. And that starts with ensuring workers have equal access to social resources in their city of employment, regardless of their background, so that they can accumulate skills and meaningful professional experiences.
Second, training and certification standards should be consistent across companies and training institutions, with an emphasis on practical abilities rather than theoretical knowledge. Moreover, while companies and vocational colleges should be encouraged to collaborate on internship programs as a means of merging theory and practice, we must take care to prevent trainees from being exploited as a source of cheap labor.
Finally, in the interests of decreasing the cost of formal recruitment and curbing the shift to “flexible employment,” China must regulate unfair collusion between companies while incentivizing them to provide workers with higher and more equal wages.
Translator: Lewis Wright; editors: Cai Yiwen and Kilian O’Donnell; portrait artist: Wang Zhenhao.
(Header image: Workers at a LCM production line in Hunan province, Nov. 18, 2021. VCG)